The Lübeck-based company CellTec Systems sees itself as the first German full-service provider for industrial cell production. Anyone wanting to get into cellular agriculture can obtain all the building blocks for production here: Cells, nutrient solution, bioreactors, and even training and consultancy services. What makes the company, which is a spin-off of the Fraunhofer-Gesellschaft and the University of Lübeck, so special is its 25 years of expertise in cell cultivation. CellTec Systems has also developed a special bioreactor with hydrogel capsules designed to cover the immense space requirements of dividing cells.
Professor Dr Charli Kruse, co-founder and scientific director of CellTec Systems, talks to us in an interview about why he describes his colleagues and himself as cell whisperers, how the patented reactor with hydrogel capsules works and why he himself does not want to get involved in cultured meat production.
Let’s imagine that someone wants to get involved in the cultured meat industry and now goes on a kind of shopping spree at CellTec Systems. The first thing the person needs is cells. Which ones can they get from you?
We have cells from around 30 animals in our cell bank. These include cells from pigs, goats, rabbits and sheep, for example. We often have different breeds – as with the cattle, which come from Schleswig-Holstein and France, among other places. Various fish cells from eel, trout and sturgeon are also part of the range.
Your scientific career began in marine biology. Is that why the cultivation of fish meat is particularly close to your heart?
Yes, because we need to take the pressure off the oceans and protect fish stocks. Animal husbandry must generally be carried out at a sensible ecological level. I’m not vegan, but animals need to be kept properly and we need to move away from factory farming on a global scale.
Do you believe that cultured meat can win over consumers?
Whether it is slaughtered or cultured meat will probably make no difference to the consumer in terms of the sensory experience. I am convinced that the flavour will be identical. The odour is already the same. For example, if we cultivate rabbit cells in sufficient quantities, after they have been concentrated and dried, the original odour will be of rabbit hutch.
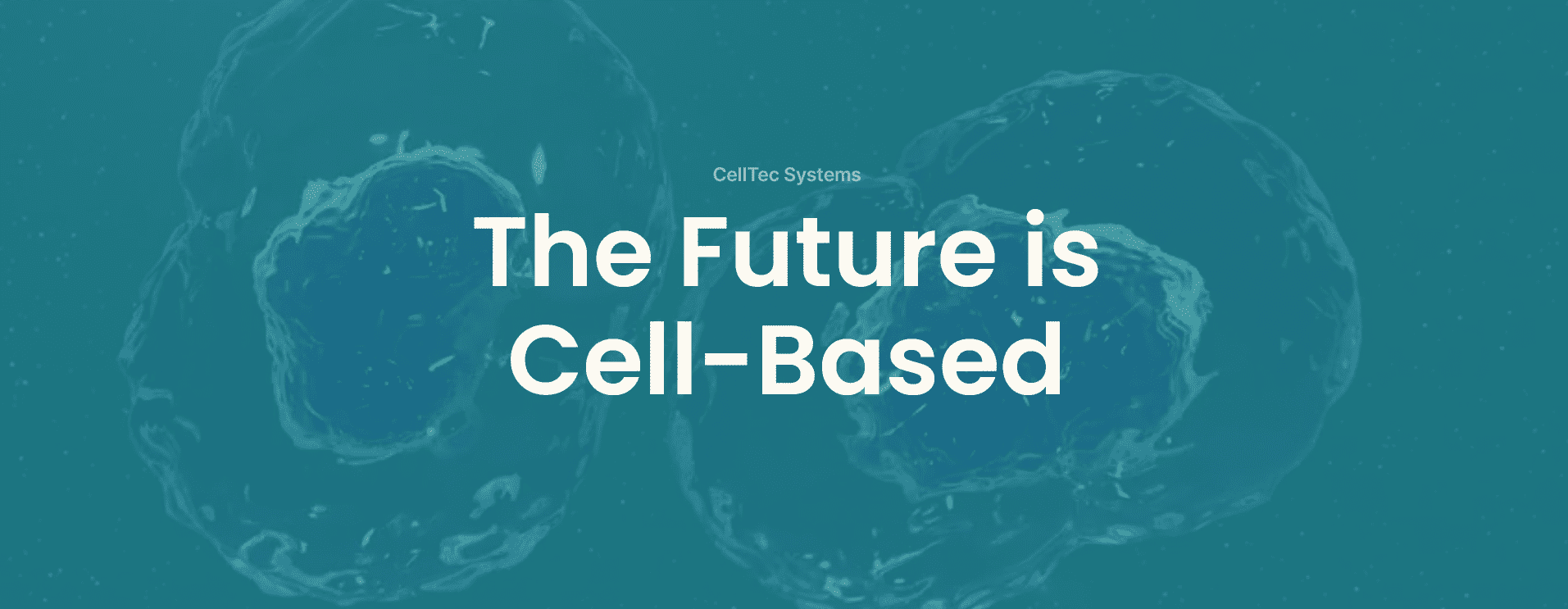
Where do you get the cells from? Is it correct that CellTec Systems even performs biopsies on animals for its customers?
Basically yes, but until now this has not been necessary. Because only small pieces of tissue are required for the cell cultures, unused parts from the abattoir are often sufficient. That’s better than throwing them away. That’s how it used to be done: everything from the animal was used – from the skin to the bones. Ear biopsies are another source of cells. Calves are given ear tags on farms. We obtain a sample from the resulting punch, i.e. the punched-out tissue. We are currently optimising the ear biopsy procedure. However, there are many other ways of obtaining tissue with sufficient cells: For example, the umbilical cord, the placenta and remnants of animal surgery are also suitable for this.
How big does the tissue have to be?
Pieces one to two millimetres in size are completely sufficient. The material is then shredded mechanically and with the help of enzymes. More than 100,000 cells can usually be removed from a biopsy. Some are kept, some are frozen. It is important to me to work with natural and not genetically modified cells – especially so as not to jeopardise public acceptance.
The cells obtained are extremely small. How long do they have to grow until enough meat is produced?
A single cell weighs about one to two nanograms. A nanogram is one billionth of a gram. But after 50 days, one to two tonnes of biomass can be cultivated from it. It works like the legend of the chessboard and the grain of rice.
What happens in this fairy tale again and what does it have to do with cell growth?
In the story, a wise Brahmin is allowed to demand a favour from the ruler of his country for inventing the game of chess. He asks – seemingly modestly – for rice. He uses the chessboard to describe the amount he wants. The ruler should place a grain of rice on the first square. On the second square, double the amount, i.e. two grains. On the third square, double the amount again, i.e. four grains. This principle should be followed until the last square of the chessboard. At first, the ruler and his scholars laugh at this supposedly pitiful request. But in the end, so many grains of rice are collected that the ruler is unable to fulfil the wish. The fairy tale illustrates the nature of exponential growth. Because cells also double again and again in this way, they also reach gigantic quantities after a very short time.
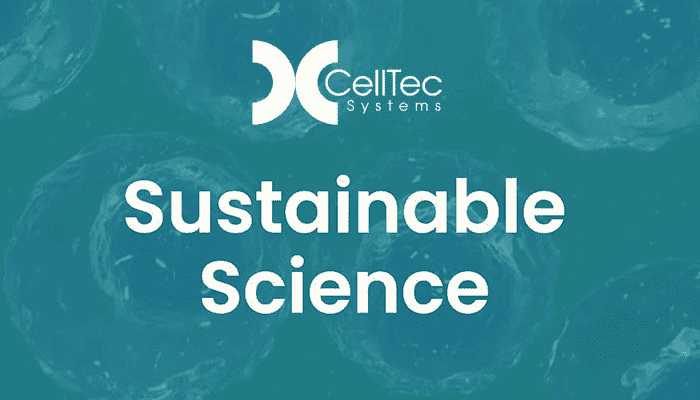
How can you imagine the consistency of the cell mass obtained?
When cultivating cells, you don’t end up with solid chunks, but rather a kind of highly concentrated protein soup. Cells do not have a solid supporting skeleton. This is why many companies also rely on hybrid products. Cultivated animal cells are mixed with a plant base to provide structure. This is because cultured meat companies still face challenges when it comes to achieving a firm texture like that of a cutlet. Currently, it is mainly minced meat and pâté-like consistencies that are feasible. Producing a steak from cells alone is the highest art.
What influence does the nutrient solution have on the cell culture?
The nutrient solution in which the cells are to grow is of course also decisive for the success of the culture. We want to provide our customers with exactly the right mixture for the respective cells – of course without foetal calf serum, otherwise you can forget about acceptance by the population. We would like to have the nutrient solution supplied by an external partner. Corresponding co-operations are currently being established.
Let’s continue the virtual shopping tour: the customer has decided on the cells and the nutrient solution has also been ordered. Now he still needs a bioreactor in which to grow the whole thing. These reactors are already available on the market…
Of course, the containers are also available elsewhere. But they come from the pharmaceutical sector and are not designed for other industrial cell cultures like we need. You can’t produce tonnes of biomass in them without the costs exploding. CellTec Systems has therefore come up with something special for the reactor technology: Firstly, our patented reactor consists of different modules and is available in several sizes. Secondly, hydrogels are used for cell propagation. This clever feature makes it possible to fulfil the immense space requirements of the cells.
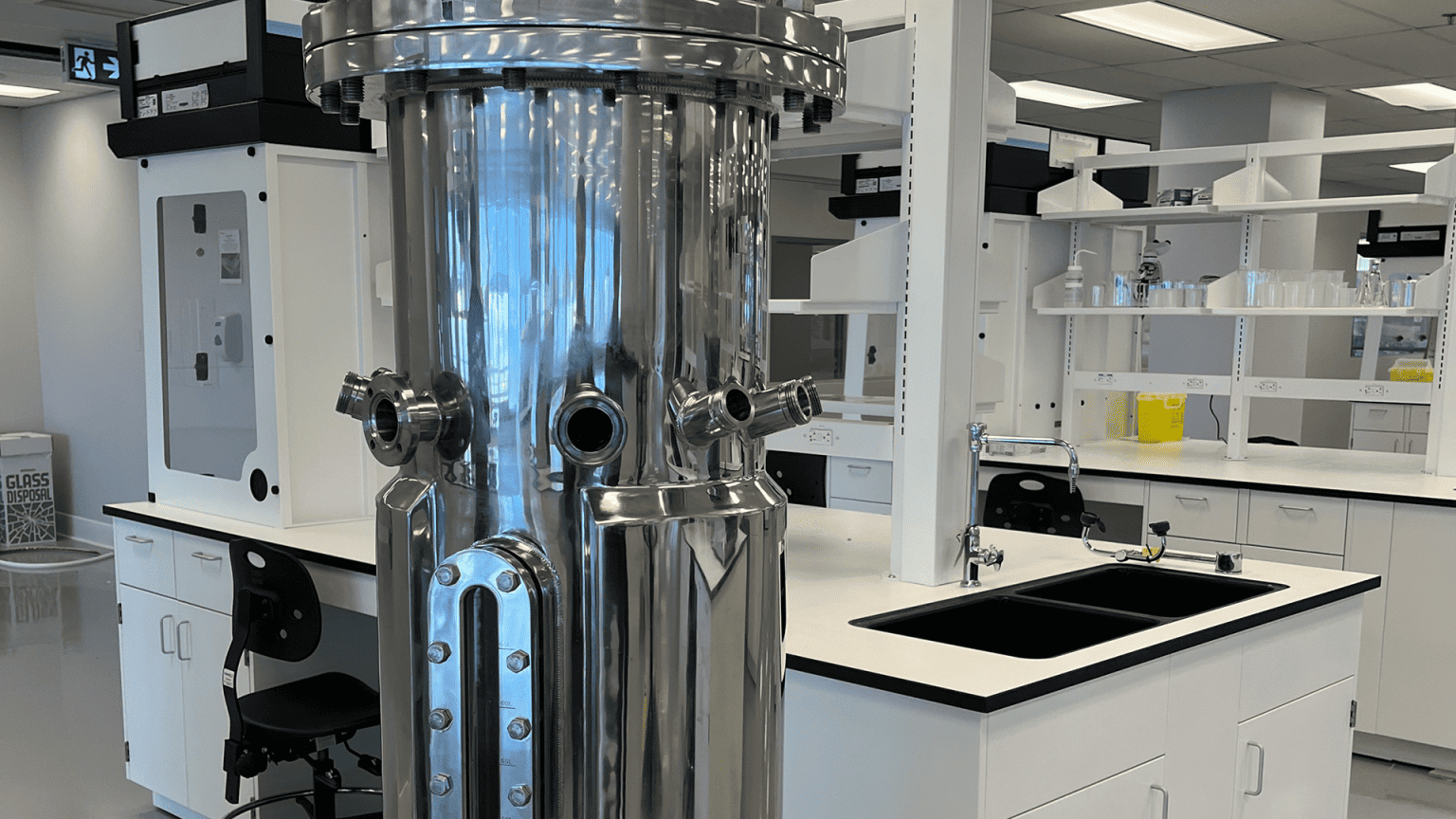
How exactly does this work?
Cells need a surface to adhere to. If you fulfil this wish, they duplicate themselves until they bump into another cell. And that’s a good thing. Let’s think of a cut in our skin, for example. In the case of an injury, the cells stop dividing as soon as the wound is closed. In order not to interrupt the growth of a culture, the cells must not touch each other, so you need a lot of space. If I want to obtain a steak in this way, I need the area of half a volleyball court. Now comes the trick: instead of proceeding in two dimensions, you add a third dimension. I have to create the culture in 3D, not 2D. That’s the crux of the matter.
And what is the purpose of the hydrogel capsules?
To create the third dimension, we offer the cells hydrogel capsules. These little balls can be imagined as the pearls in a bubble tea. The cells multiply in the miniature balls, which provide a much larger surface area thanks to their internal structure. Even if the cells bump into each other at some point, this does not hinder the activity in the neighbouring bubbles. Once growth is complete, the bubbles are dissolved and the cells remain.
The question of sterility remains. Can cell cultures be kept sterile in bioreactors? Critics of cellular agriculture ultimately doubt that this is possible.
I can understand the scepticism, but ultimately I don’t see a problem. At the moment, cells are still propagated in the laboratory in petri dishes and with the addition of antibiotics as a precaution. However, closed reactor systems could be kept sterile. There are already companies that have kept cell cultures clean in this way for three months and longer. And three months is quite enough.
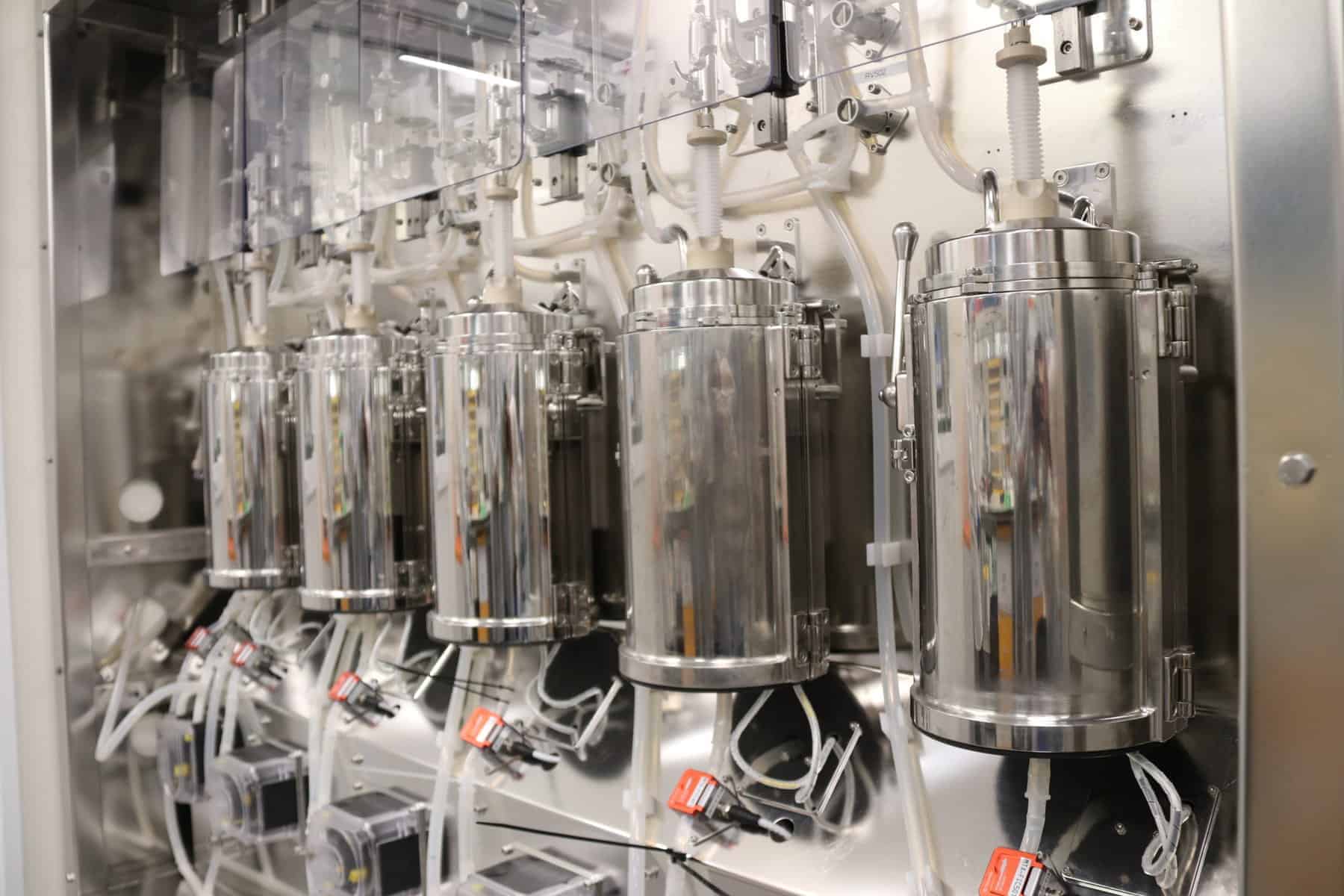
Let’s summarise: Our shopping trolley now contains cells, nutrient solution and a bioreactor system with hydrogel capsules. Can any company now get started with cultured meat breeding?
As the handling of biological cell cultures is anything but trivial, the results often fall short of expectations. Very often there is a lack of proven expertise and skills. This is why companies can have their employees trained by CellTec Systems in cell culture courses online or in person. Update courses ensure that staff knowledge is always up to date. We offer training courses as workshops at our premises in Lübeck, but we can also come to your company.
So your company has the necessary knowledge, machines, materials and patents – why doesn’t CellTec Systems get into cultured meat production itself?
That is a question of capacity. Firstly, you would have to invest more than 100 million here. That’s not on our scale. Secondly, I am a scientist and developer in heart and soul. Industry and production is a different world. Anyone who gets involved here is out of the science business.
Why is it so important to you to make your own expertise available to industrial cell multiplication?
For me, this technology is the future. It’s not just about food. We have a completely new renewable source of raw materials, similar in importance to crude oil. For example, we can not only produce meat for human consumption, but also animal feed. For the cosmetics industry, alternatives to animal testing could be offered and for the pharmaceutical industry, possibilities for rapid vaccine or protein production. In future, we could use cells to do many of the things we have needed living animals for up to now. I think that’s gigantic.
Further information: celltec-systems.com
This interview was conducted and provided by journalist Susanne van Veenendaal. As part of a book project on cultured meat, on which Susanne van Veenendaal is working together with Christoph Werner and Bastian Huber from cultured-meat.shop, she is talking to various German companies, researchers and initiatives in the sector.