GEA, a global leader in engineering systems for the food, beverage, and pharmaceutical industries, is unveiling what it claims to be a “technological milestone” — the perfusion platform — at the Anuga FoodTec trade show in Cologne, Germany.
The perfusion platform consists of the GEA Axenic-line bioreactors and the GEA kytero single-use separator, designed to enhance productivity and cost efficiency in cell cultivation and precision fermentation. The technology promises to level the price difference between conventional and alternative foods.
Tatjana Krampitz, Head of New Food Technology Management at GEA, comments, “We see perfusion as one of the most promising technologies because it cuts the production cost of alternative proteins on several fronts.”
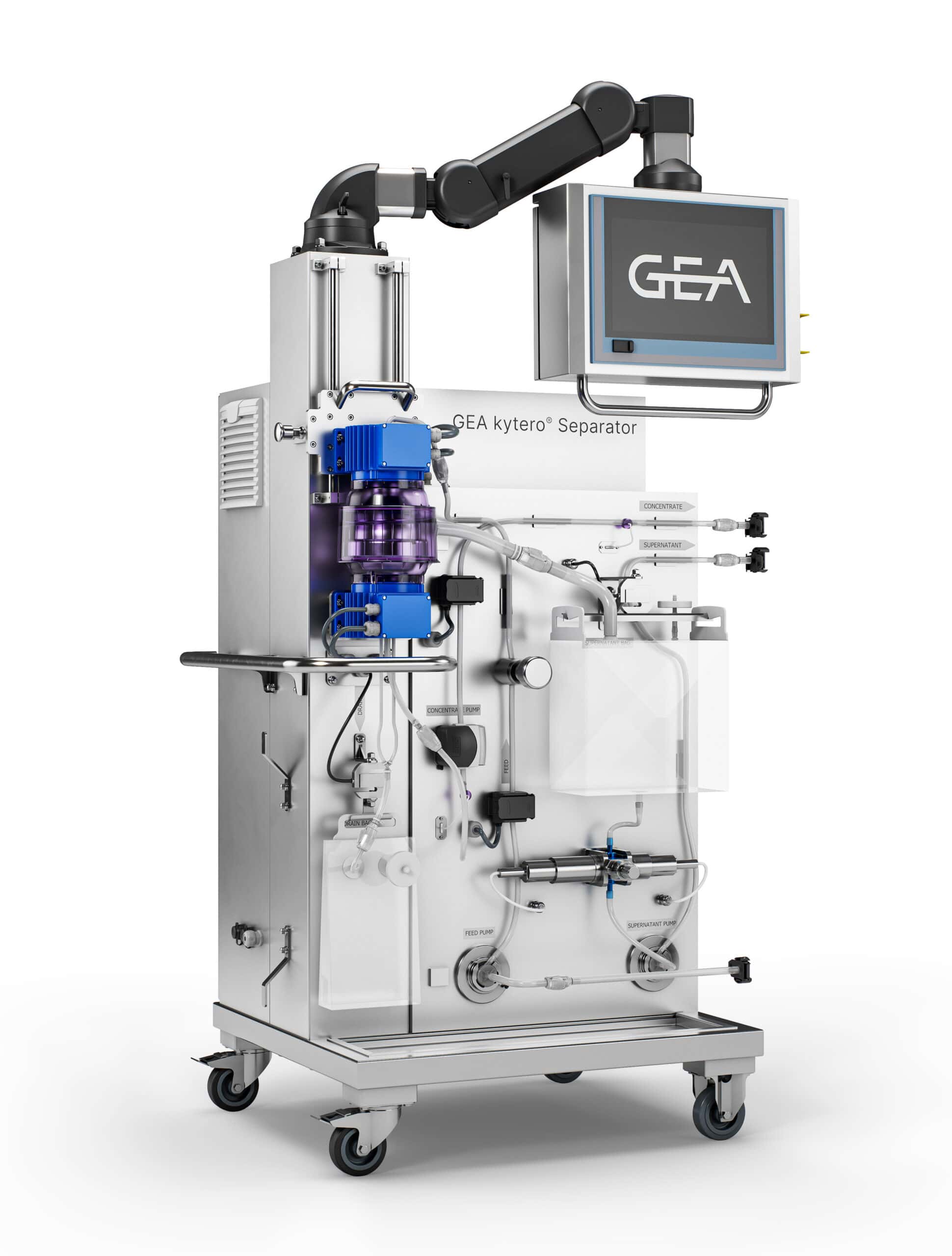
Separating the cells
GEA’s perfusion technology separates cells from already depleted nutrient solution and then returns them to the bioreactor with a “fresh” batch of medium in sterile conditions. The intent is to remove growth-inhibiting metabolites such as ammonium and lactate from the growth medium.
This innovative process enhances productivity and cell density and ensures reproducible product quality, a key criterion for the regulatory approval of novel foods. In addition, it allows reprocessing media (reusing and purifying), a feature that significantly lowers the production costs and, in turn, the price of final products.
GEA explains that its single-use separator, a component widely used in the pharmaceutical industry, is crucial in pilot processes. It allows startups to validate their product ideas without needing complex cleaning and sterilization facilities.
“What the market currently needs are reliable pilot plants that are quick to set up and meet industrial standards. Our single-use separators enable start-ups in particular to work under sterile conditions, which helps them surmount a major challenge,” Krampitz adds.
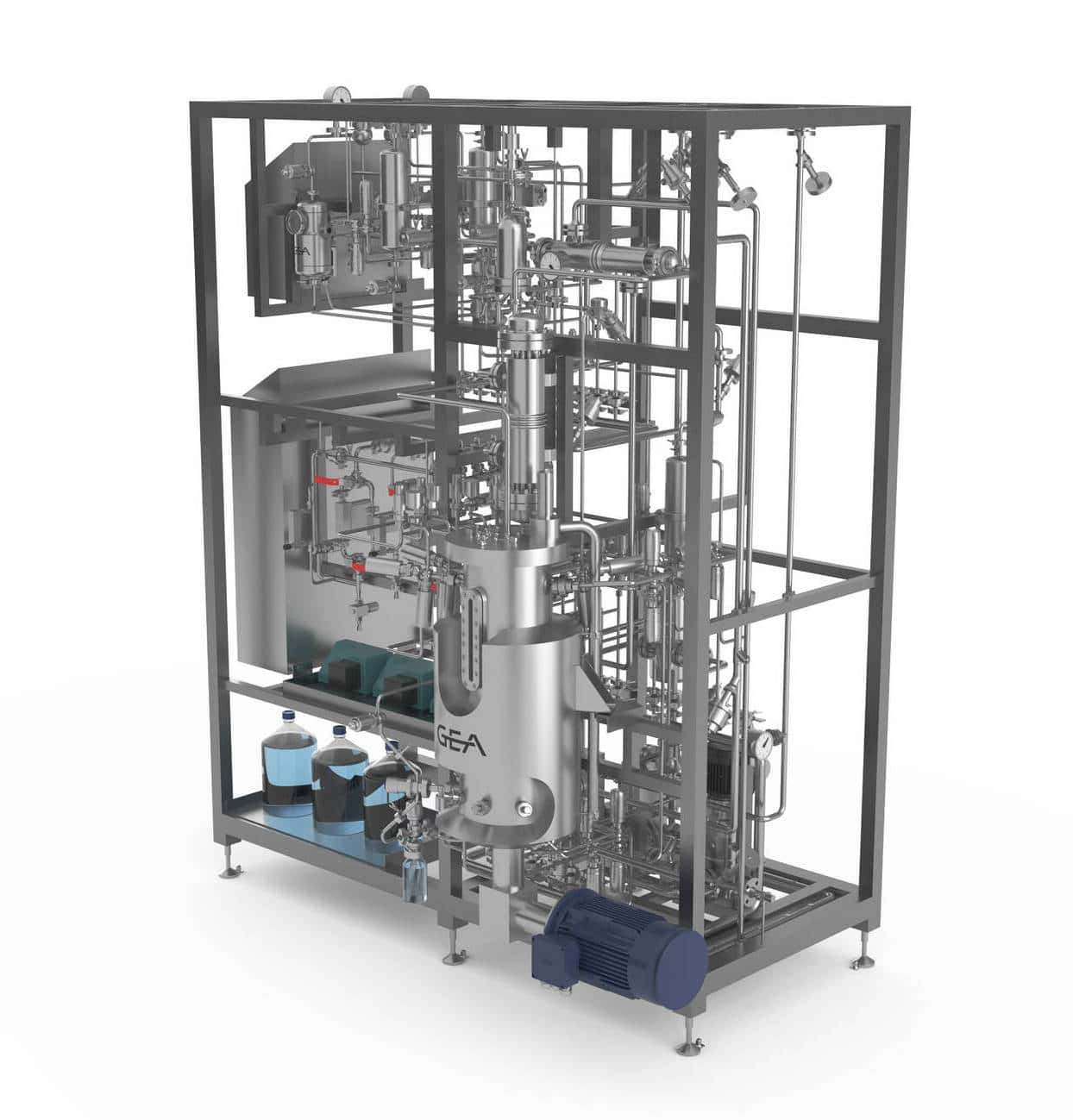
Improving capacity
According to GEA, perfusion is an essential innovation for upstream and downstream processes because it allows for continuous operation of bioreactors and material flow, thus improving capacity utilization.
“If we were to transfer the production capacity requirements for new foods one-on-one onto conventional process lines, the resulting plants would be huge”
GEA experts estimate that perfusion could reduce bioreactor size, media, and space requirements by 10%, ultimately driving down production costs.
Krampitz adds, “If we were to transfer the production capacity requirements for new foods one-on-one onto conventional process lines, the resulting plants would be huge. Perfusion lets us grow cells in a much smaller space. In the long term, this technology will blaze a trail when it comes to shrinking bioreactors and hence reducing both the quantity of stainless steel needed and the nutrient and cleaning media required.”